Message |
I drilled a hole with drill size R (for 1/8" NPT threaded egt) on the left side (driver's side) MS header. The drilling was done really well on a mill and went just great. Once I got to tapping, I did everything as I was supposed to, but one thing lead to another and the tap didn't go straight in line with the drilled hole. Eventually one side had ALL the thread material, and the other side had no thread. The tap hole basically got ruined. I proceeded to reaming the hole out to slightly over 1/2", and dropped in an egt bung (I think it's stainless), and tig-welded it to the MSP manifold with a suitable filler for welding stainless to carbon steel (ER-08 filler), with surgical precision, and low heat as to not overheat the header or crack it. I beveled the opening so I got good penetration, and I did 2 passes. It looks pretty good, at least compared to a messed up tapped hole. The header barely got warm during welding, definitely no discoloration on the header/flanges, but I had to watch out so the egt bung didn't burn through, and it didn't. Can you guys look at the pics and see any reason if/why I shouldn't use this installation and whether I should get a new left MSP header (I haven't done the right side yet)? I don't think it'll crack, it's thick enough at the weld, and there is no leak but is there something I'm missing that someone else knows causing this not to work out over many cycles? 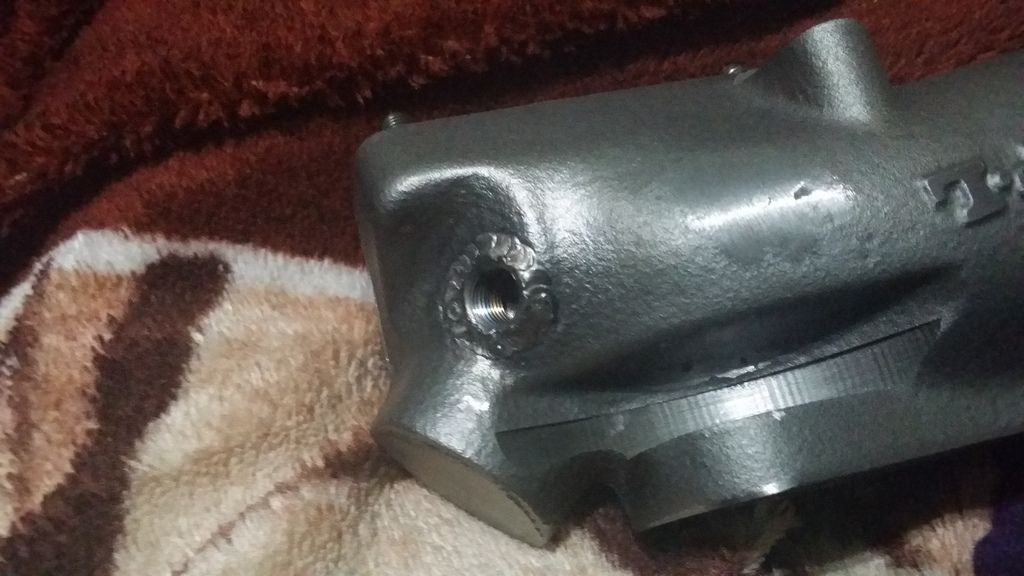
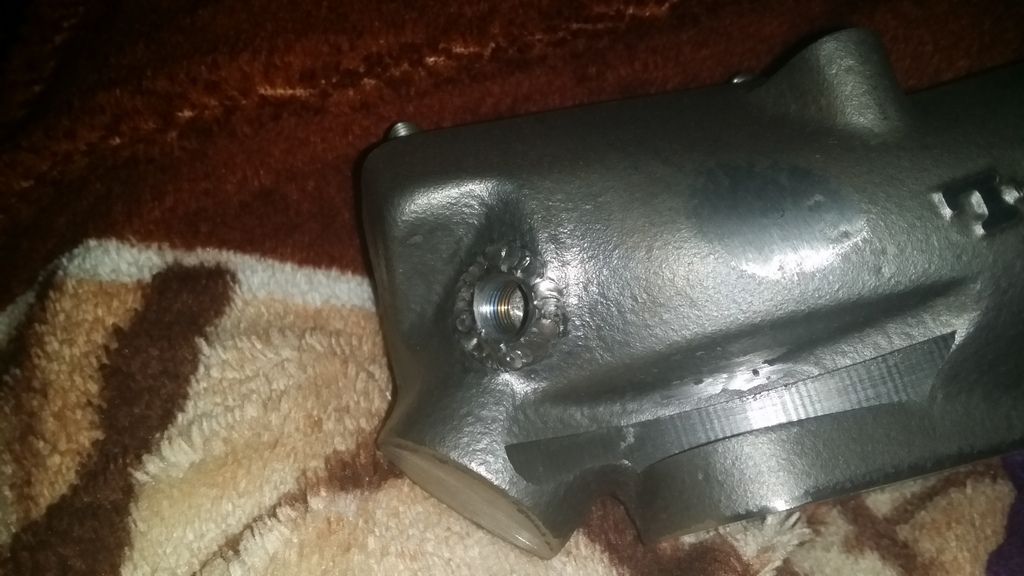
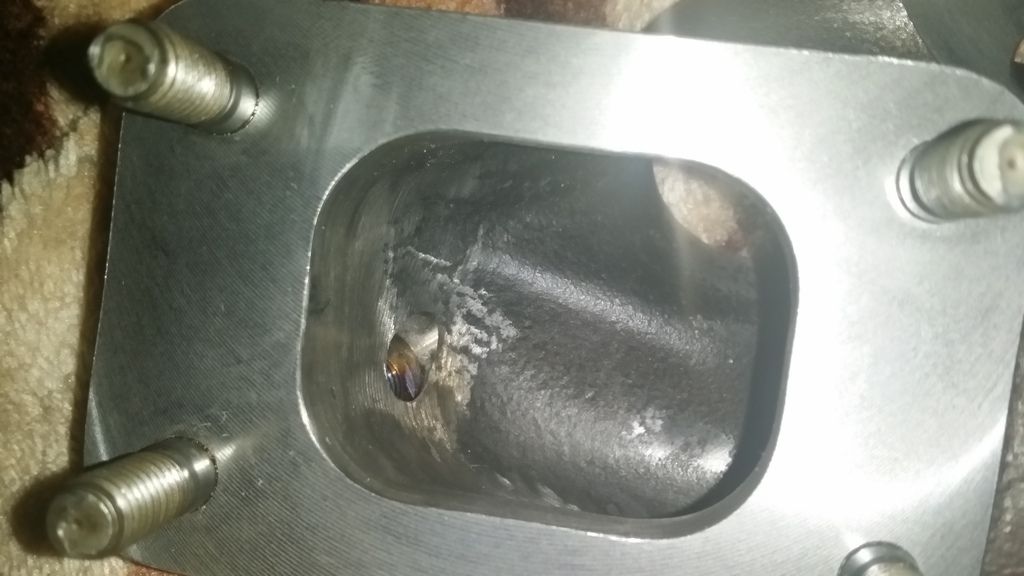
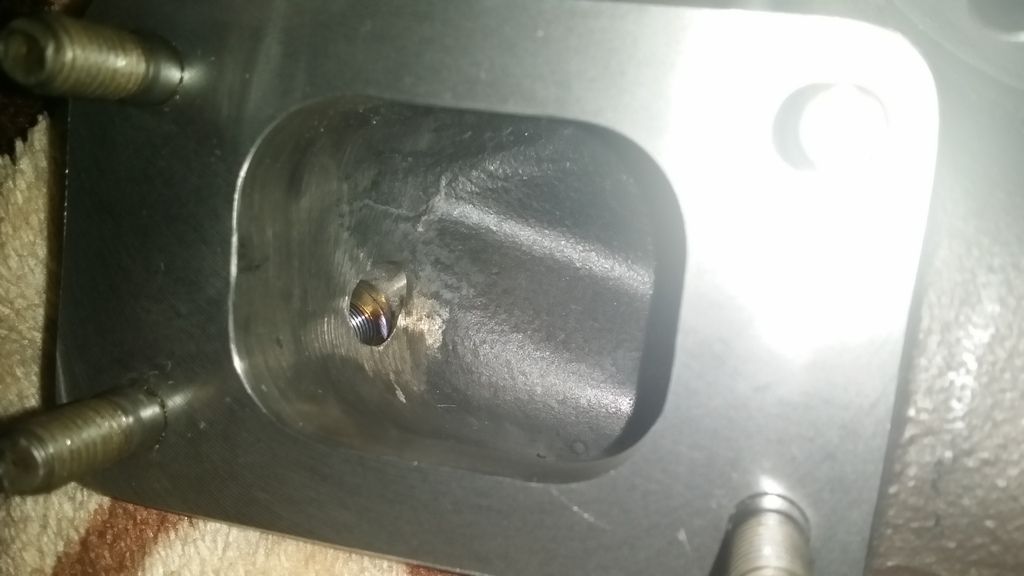
|
 |